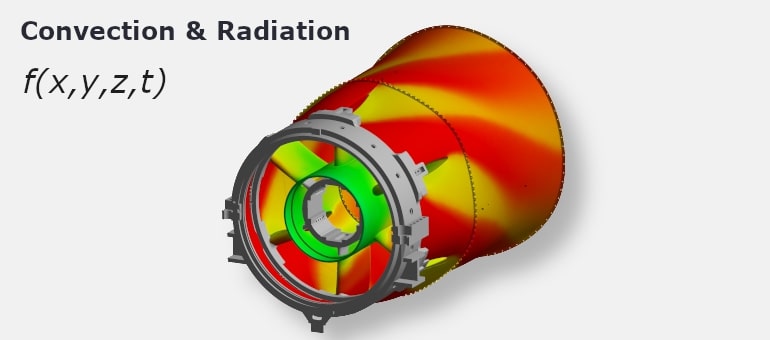
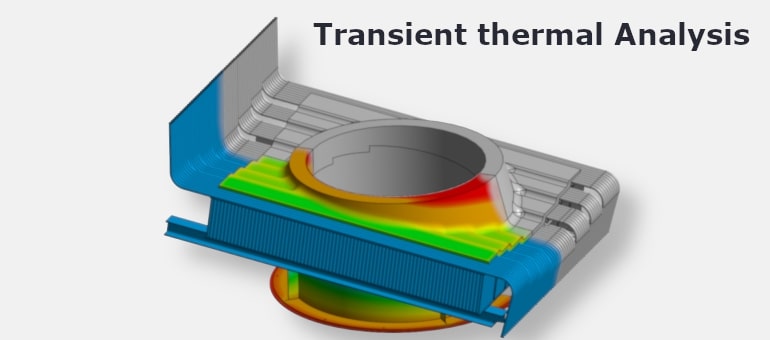

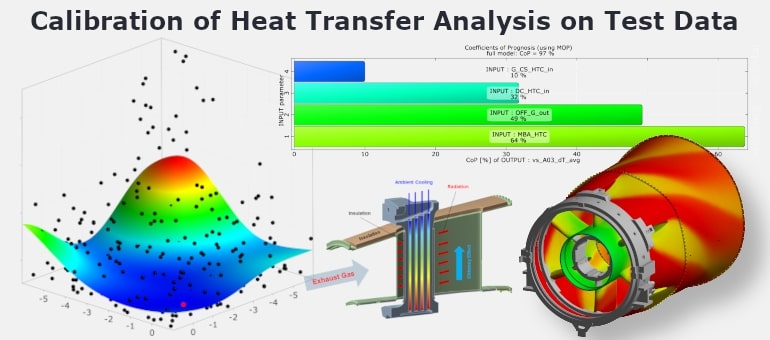
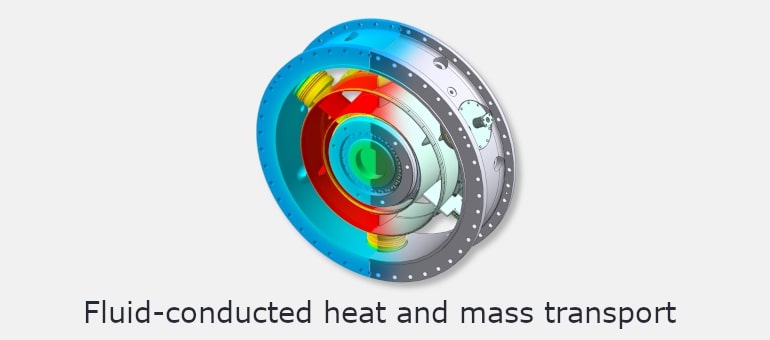
Heat Transfer
Thermal performance and integrity are ensured through comprehensive assessments under steady-state and transient conditions. Advanced simulation techniques — including conduction, convection, radiation modeling, and conjugate heat transfer (CHT) — are applied to capture temperature distributions, thermal gradients, and heat fluxes in complex components and assemblies. Applicable across all industries and thermal applications. The methodology integrates fluid-solid coupling, spatially varying boundary conditions, and time-dependent heat loading to support reliable thermal design, thermal stress prediction, and compliance with operational limits — from early design to prototype validation.
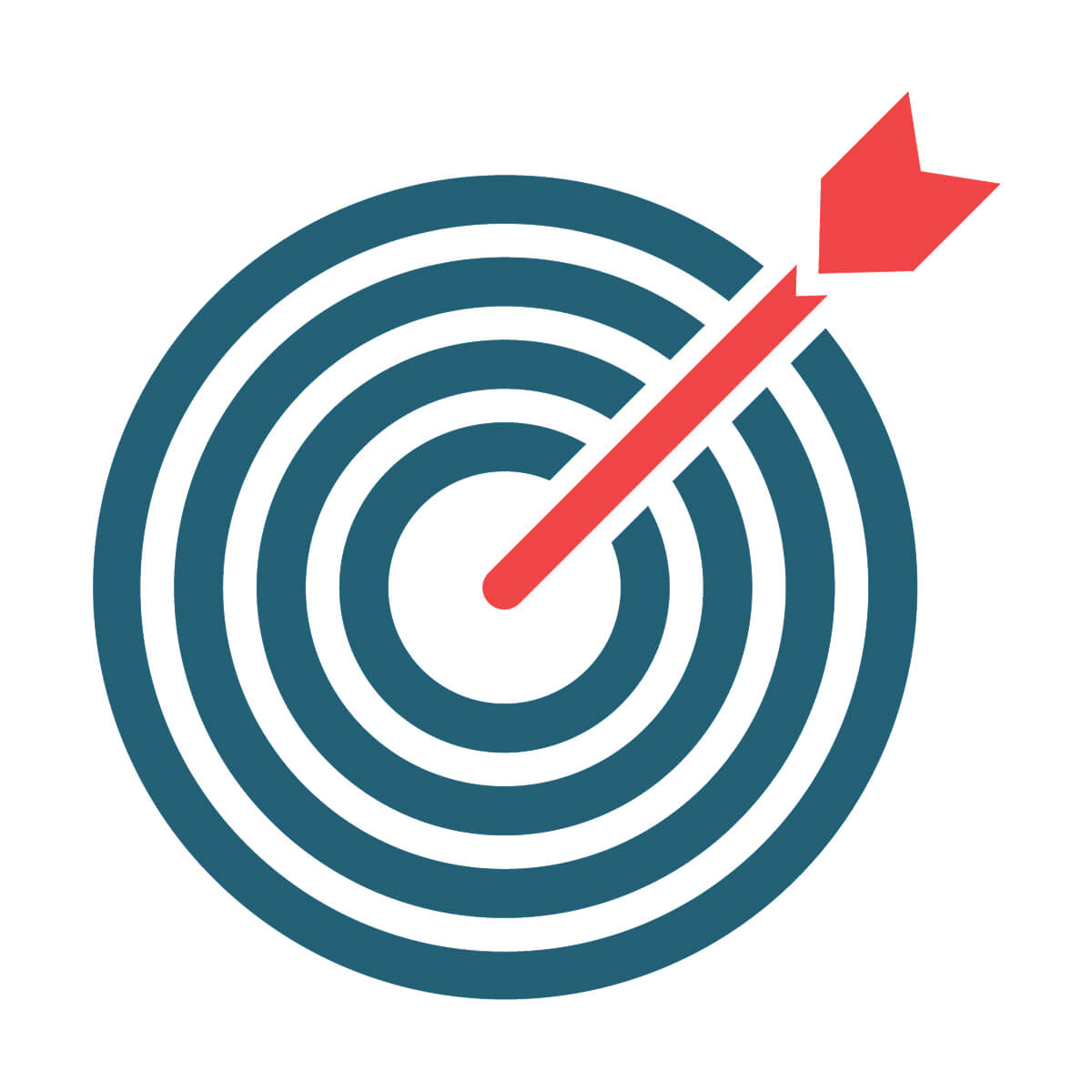
Key Capabilities
- Steady-state and transient thermal simulations — temperature distribution over time and varying operating conditions
- Conduction, convection, and radiation modeling — all major heat transfer modes, including natural and forced convection
- Fluid-conducted heat and mass transport — includes conduction and convection modeling via elements such as FLUID116
- Spatially varying boundary conditions — temperature, heat flux, and HTC defined as field inputs
- Radiation — surface-to-surface or ambient radiation including view factor modeling
- Conjugate Heat Transfer (CHT) — fluid-solid thermal interaction using CFD-derived temperature and heat flux fields
More information
Steady-state and transient thermal Analyses
Steady-state and transient thermal analyses determine temperature distributions under constant and time-varying operating conditions. Spatially varying boundary conditions — such as temperature and heat transfer coefficients — are applied using CFD results or analytical data. Radiative heat transfer is modeled using view factors to capture surface-to-surface and ambient exchange.
Example: Thermal evaluation of a turbine exhaust module during engine operation, where non-uniform convection and radiation drive critical local temperature gradients.
Fluid-conducted heat and mass transport
Fluid-driven heat and mass transport is modeled using 3D thermal-flow elements such as ANSYS-FLUID116, enabling conduction and convection within internal passages. Flow is driven by temperature or pressure differences, allowing thermal coupling with surrounding solid structures.
Example: Thermal modeling of internal cooling channels in a turbine exhaust casing, where flow-dependent heat removal is governed by local temperatures.
Conjugate Heat Transfer (CHT)
Conjugate heat transfer simulations couple fluid and solid domains to capture thermal interaction across interfaces. CFD-derived temperature and heat flux fields are mapped onto structural meshes to represent realistic boundary conditions. This approach enables accurate prediction of thermal gradients and stresses in complex geometries.
Example: Coupled thermal analysis of a bearing body exposed to oil flow, including heating from adjacent hot-gas components and radiation from nearby surfaces.