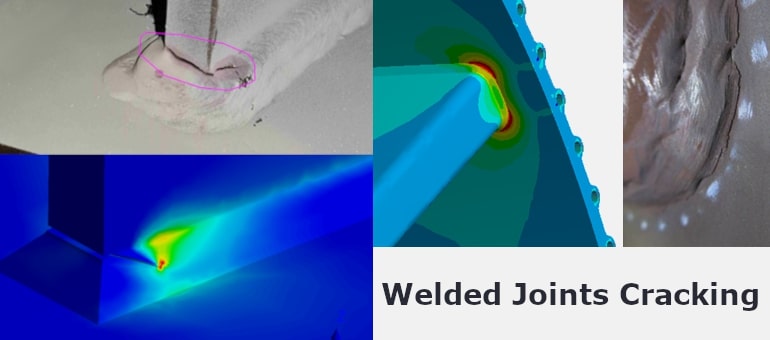
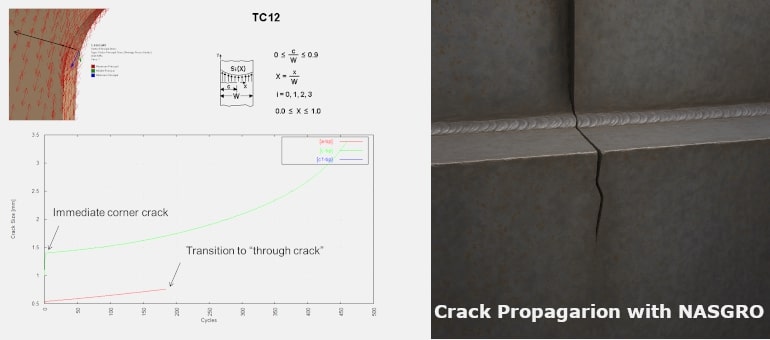
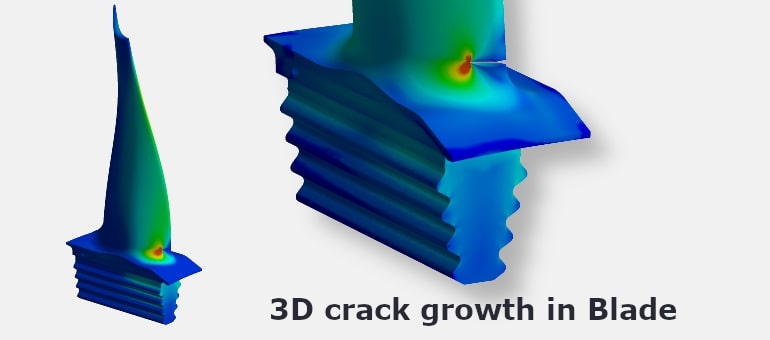

Fatigue & Fracture Mechanics
Structural durability and failure resistance are assessed using advanced fatigue and fracture mechanics methods to ensure long-term reliability under cyclic and extreme loading conditions. Capabilities include high-cycle and low-cycle fatigue analysis, crack initiation and growth prediction, and linear or non-linear fracture evaluation based on operating loads and temperature effects. Applicable across a wide range of industries and components — from welded joints and rotating parts to pressure vessels and thermal-stressed structures.
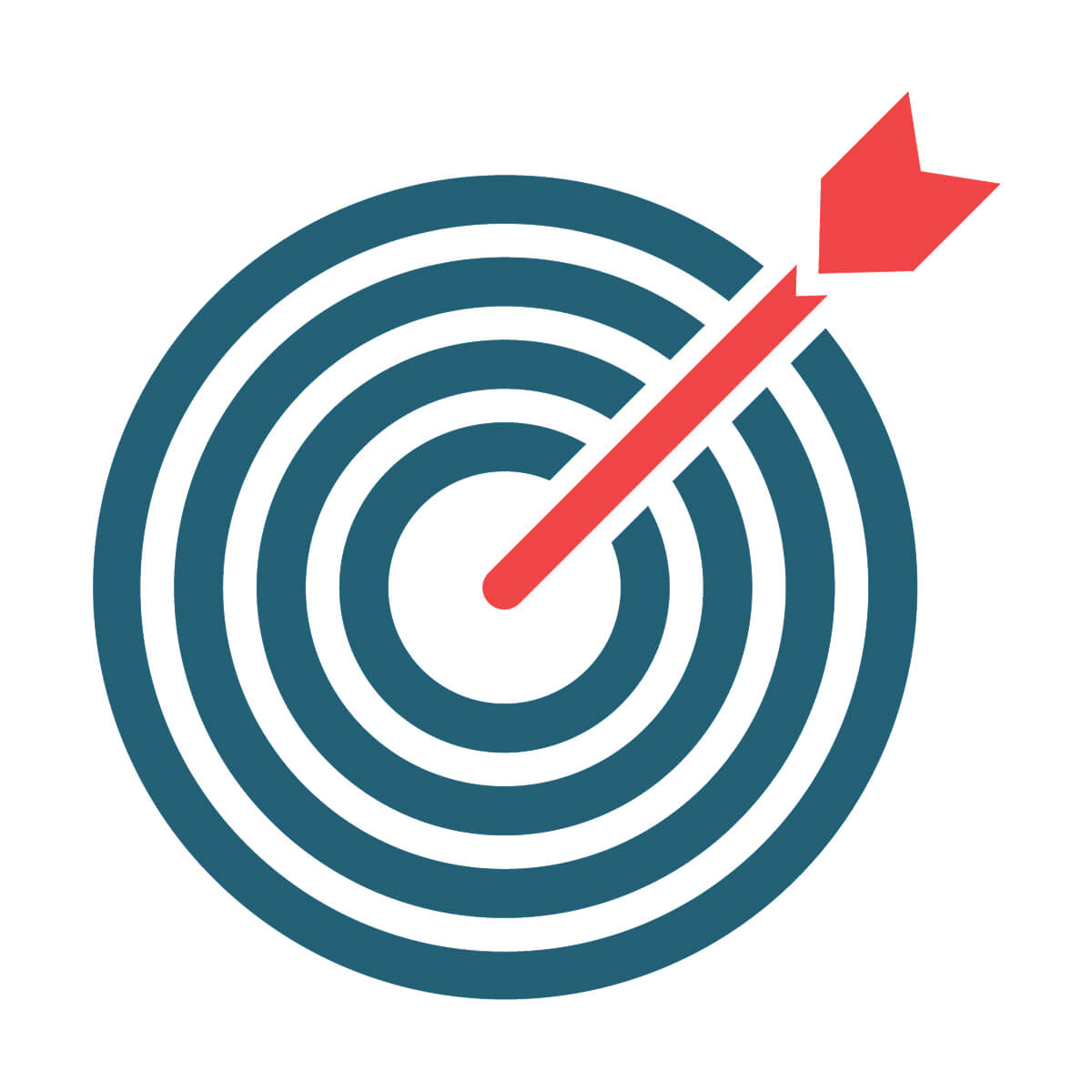
Key Capabilities
- High-cycle (HCF) and low-cycle fatigue (LCF) assessment under mechanical and thermal loading
- Fatigue evaluation of notches, welds, and geometric discontinuities
- Crack initiation and propagation modeling in welded and non-welded structures
- 3D crack propagation simulation with automated direction and growth prediction
- Fracture mechanics assessment using NASGRO or IWM VERB for crack growth and remaining life estimation (FAD)
- Thermal fatigue and creep-fatigue interaction under transient load conditions
- Compliance with design codes (e.g., ASME, EN 13445, FKM, IIW,..)
More information
Low-Cycle Fatigue (LCF) Assessment
Evaluates structural durability under high strain, low-cycle loading conditions typically caused by start-stop operations, thermal shocks, or load reversals. Material plasticity, cyclic hardening/softening, and temperature effects are considered to predict damage accumulation and failure onset.
Example: LCF life estimation of a compressor vane carrier subjected to cyclic thermal gradients during operation cycle.
High-Cycle Fatigue (LCF) Assessment
Assesses fatigue life under low stress levels and a high number of load cycles, where the material response remains predominantly elastic. Typical load cases include vibrations, acoustic excitation, or pressure pulsations. The analysis is performed using stress-life (S-N) methods, incorporating Haigh or Smith diagrams and frequency-domain evaluations.
Example: High-cycle fatigue (HCF) assessment of a compressor bearing body subjected to imbalance-induced excitations.
3D Crack Propagation Simulation
Simulates crack growth in three dimensions, accounting for local stress fields, material properties, and crack path evolution under cyclic or static loading. The method enables prediction of crack direction, growth rate, and interaction with geometry features.
Example: Thermal gradient- or mechanically driven crack propagation in a welded joint, or fatigue crack growth from a notch in a cooled turbine blade — with automated path prediction through complex geometries.
Fracture Mechanics Assessment
Evaluates structural integrity in the presence of cracks using linear-elastic or elastic-plastic fracture mechanics principles. Stress intensity factors, crack driving forces, and failure assessment diagrams (FAD) are used to estimate critical crack sizes and remaining life.
Example: Remaining life assessment of a pressure vessel nozzle with a surface crack using NASGRO or IWM VERB.